Bravo
If ARM was an arm, BRN would be its biceps💪!
In this extract, Paul Karazuba, vice president of marketing at Expedera, discusses power consumption as being the major issue to resolve in terms of reaching L5 full autonomy. He reckons it will require between 1000 to 3000 TOPS for a vehicle to reach Level 5 full autonomy.
We all know that reducing power consumption is right up Aida's alley. I wonder how many AKIDA's would be required to achieve 1000 TOPS hence solving Paul's problem?
EXTRACT
Putting all of these new pieces together takes time, however. Paul Karazuba, vice president of marketing at Expedera, believes much needs to be done to get to full autonomy, starting with much faster and more energy-efficient processing of an enormous amount of streaming data. “Simply from a hardware perspective, the platforms that would be required to deploy L5 in a car don’t exist, and nor do today’s solutions realistically scale to meet L5,” he said. “L5 is going to require a certain amount of AI processing. It’s probably going to be, depending on who you talk to, between 1,000 and 3,000 tera operations per second (TOPS) of processing power. Today’s most advanced solutions for AI processing that one would find in a car is about 250 TOPS.
Fig. 2: The role of artificial intelligence in self-driving vehicles. Source: Expedera
At that level, says Karazuba, the processor consumes about 75 watts of power, which creates significant scaling problems. “If you look at the scaling that’s required, those chips will have to scale by a matter of 4 to 12X in performance, which means the associated scaling of power. Seventy-five watts is about as hot as you can run a chip before you actively need to cool it, and automakers have signaled they have no desire to actively cool electronics in cars because it’s expensive and it adds weight.”
Power constraints
Even if it were possible to scale current solutions to 3,000 TOPS, he said, doing so would consume up to 1% of the battery on one of today’s electric cars. Karazuba said one workaround is putting multiple chips next to one another, but doing so creates both space and cost issues.
“With today’s silicon, you’re talking multiple hundreds of dollars — probably approaching $1,000 per chip — and you’d have four of those in a car, or maybe 12 of those in a car. You also can’t take a chip that’s already pretty darn big and grow it by 4X or 12X. It’s going to have to go to disaggregated processing, either moving processing to multiple places within the car or moving to something like a chiplet model.”
That’s only part of the cost. All of these new features and capabilities require power, and in electric vehicles that power comes from batteries. But battery technology is only improving at a rate of about 5% to 6% per year, while demands for processing more data faster are exploding, creating a gap that widens as more autonomy is added into vehicles.
semiengineering.com
We all know that reducing power consumption is right up Aida's alley. I wonder how many AKIDA's would be required to achieve 1000 TOPS hence solving Paul's problem?
EXTRACT
Putting all of these new pieces together takes time, however. Paul Karazuba, vice president of marketing at Expedera, believes much needs to be done to get to full autonomy, starting with much faster and more energy-efficient processing of an enormous amount of streaming data. “Simply from a hardware perspective, the platforms that would be required to deploy L5 in a car don’t exist, and nor do today’s solutions realistically scale to meet L5,” he said. “L5 is going to require a certain amount of AI processing. It’s probably going to be, depending on who you talk to, between 1,000 and 3,000 tera operations per second (TOPS) of processing power. Today’s most advanced solutions for AI processing that one would find in a car is about 250 TOPS.

Fig. 2: The role of artificial intelligence in self-driving vehicles. Source: Expedera
At that level, says Karazuba, the processor consumes about 75 watts of power, which creates significant scaling problems. “If you look at the scaling that’s required, those chips will have to scale by a matter of 4 to 12X in performance, which means the associated scaling of power. Seventy-five watts is about as hot as you can run a chip before you actively need to cool it, and automakers have signaled they have no desire to actively cool electronics in cars because it’s expensive and it adds weight.”
Power constraints
Even if it were possible to scale current solutions to 3,000 TOPS, he said, doing so would consume up to 1% of the battery on one of today’s electric cars. Karazuba said one workaround is putting multiple chips next to one another, but doing so creates both space and cost issues.
“With today’s silicon, you’re talking multiple hundreds of dollars — probably approaching $1,000 per chip — and you’d have four of those in a car, or maybe 12 of those in a car. You also can’t take a chip that’s already pretty darn big and grow it by 4X or 12X. It’s going to have to go to disaggregated processing, either moving processing to multiple places within the car or moving to something like a chiplet model.”
That’s only part of the cost. All of these new features and capabilities require power, and in electric vehicles that power comes from batteries. But battery technology is only improving at a rate of about 5% to 6% per year, while demands for processing more data faster are exploding, creating a gap that widens as more autonomy is added into vehicles.
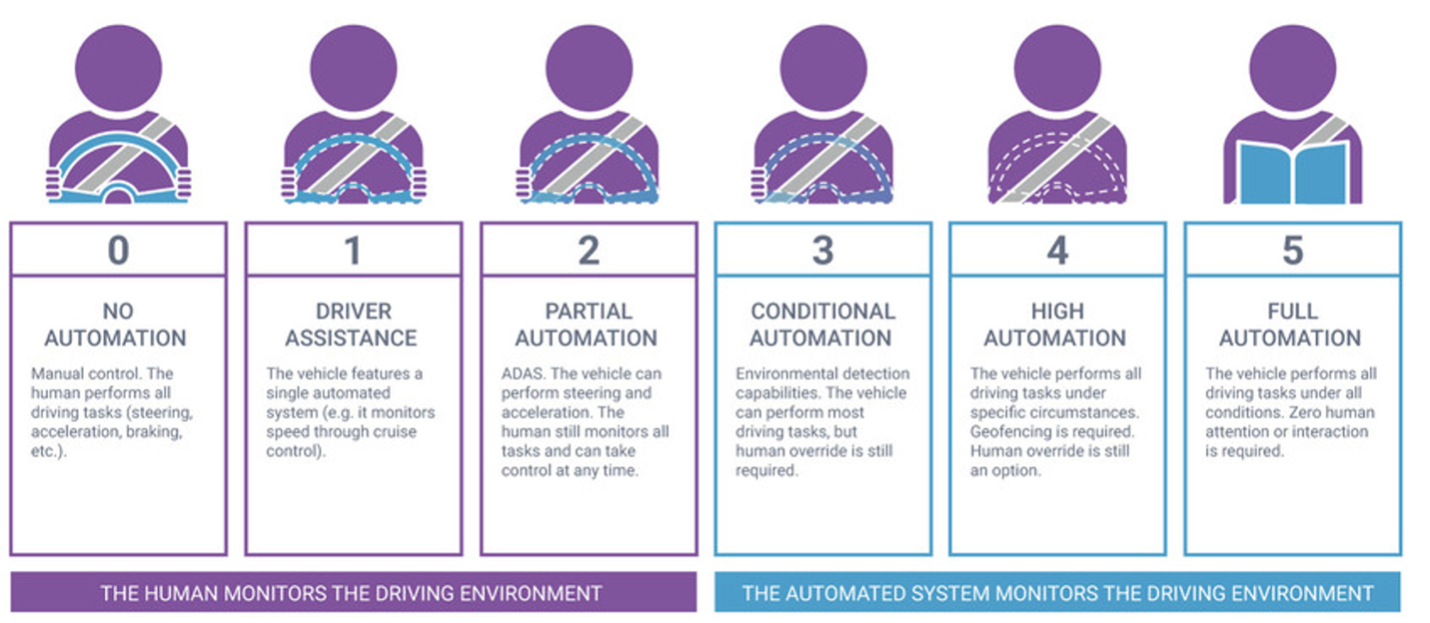
Where Are The Autonomous Cars?
L5 vehicles need at least 10 more years of development.
