BaconLover
Founding Member
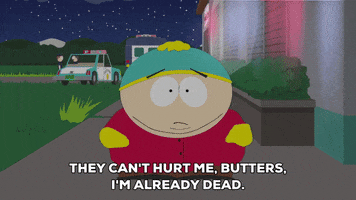
Exactly.. leave us alone, we are already dead
Don't expect too much.Thanks for that
So that gives the states the first dibs on price. So Tuesday will be very interesting.
So excited to see what the future may have install for us all.
ok thanks Frangipani! i seemed to have seen a 9am pt but must have been seeing things. ok so 8am pt as per their website and 4pm gmt so 1am bris syd melb 10May.Hi @MDhere and @Food4 thought,
the ARM tech talk will be held on May 9th at 8 am Pacific time, so that actually means May 10th at 1 am (!) in Sydney/Melbourne/Brisbane.
Just have a look here, whenever you are unsure:
![]()
World Clock & Time Converter
Effortless time conversion and world time. Schedule conference calls, webinars & online meetings, plan travel and track flight arrival time across time zones.www.worldtimebuddy.com
View attachment 35875
I hope it's a nice birthday present!ok thanks Frangipani! i seemed to have seen a 9am pt but must have been seeing things. ok so 8am pt as per their website and 4pm gmt so 1am bris syd melb 10May.❤ Alarms set!
Hopefully they can talk Arm into releasing a little nugget for us.ok thanks Frangipani! i seemed to have seen a 9am pt but must have been seeing things. ok so 8am pt as per their website and 4pm gmt so 1am bris syd melb 10May.❤ Alarms set!
Hopefully they can talk Arm into releasing a little nugget for us.
Hence Friday sp riseIncoming announcement not yet released.
![]()
Socionext Europe • BrainChip and Socionext Provide a New Low-Power Artificial Intelligence Platform for AI Edge Applications
ALISO VIEJO, Calif.--(BUSINESS WIRE)-- BrainChip Holdings Ltd (ASX: BRN), a leading provider of ultra-low power high performance AI technology, today announced…www.eu.socionext.com
Almost perfect now, except (sorry for being pedantic) the talk is going to be at 4 pm BST (British Summer Time) and thus technically at 3 pm GMT (Greenwich Mean Time aka British Winter Time).ok thanks Frangipani! i seemed to have seen a 9am pt but must have been seeing things. ok so 8am pt as per their website and 4pm gmt so 1am bris syd melb 10May.❤ Alarms set!
Thanks.
Hence not Fridays rise in SPThanks.
The FED last week raised interest rates .25%, but there was some clear language from JP that its very possible that it might be the last.Hence not Fridays rise in SP
Not sure if everyone has seen this demo from SocioNext on this page. Its clear they are very happy with the sensor fusion and low power solutions of Akida for all their senor inteligence going forward. They are a tier 1 auto supplier using Akida as the SOC solution for the digital car of the future.
They do not have a licence agreement but they have noted that they have partnered with BRN. it still confuses me the different entitlements that a license and a partnership gets a customer but this is clearly a relationship that is close to bringing in ongoing revenues.
![]()
Automotive Custom SoC Technologies and Solutions
Socionext’s advanced automotive custom SoC solutions are designed to help OEMs and tier-one automakers achieve differentiating technologiessocionextus.com